Todd@RUPES
Just a regular guy
Advanced Concept: Does the polishing pad have to rotate to remove paint defects when using an DA Polisher.
Dual-Action Polishers are unique machines that rely on a multitude of simple physics in order to perform their job. Their job? In our world, DA (Dual-Action) polishers are used to polish paint. Polishing paint refers to the ability to remove material (in this case microscopic amounts of paint) in order to create a more level surface that reflects evenly. What gives a DA polisher its name is it's ability to move the pad in two different paths at the same time: In an eccentric or orbital pattern as well as a rotational pattern.
Random Orbital DA polishers only drive the orbital movement of the backing plate and pad. The rotation of the pad is a secondary movement, which is created by the inertia of the orbiting pad.
To understand the above concept imagine that you are holding a string straight above your head. Attached to the end of the string is a tennis ball. In order to swing the ball in a circle above your head you begin to spin your hand in tiny circles. Since you cannot dislocate your wrist and rotate it, you move your arm in an orbital motion. The inertia from your orbiting hand causes the ball to rotate above your head.
Another (more accurate) analogy is bicycle pedals. Bicycle pedals are attached to an arm that runs from center axis to the pedal. They orbital around the center axis because of the offset. If you jack a bicycle in the air by the frame (or lift up on the seat) so that the drive wheel is not touching and begin to 'pedal' the bike quickly with your hand you will notice that the pedal on the opposite side of the bike will begin to spin (in addition to orbiting around the axis).
The picture below illustrates the difference between an orbital movement and a rotational movement.
When we are polishing paint, in simple terms, we are trying to convert the the energy created by the motor of the machine into friction that removes paint. With a Dual-Action polish the energy is transferred to the drive arm (which orbits around the axis of the motor), through a bearing (which allows the pad to spin independently of the motor), to the backing plate, through the hook and loop, through the pad, and finally to the abrasives which are attached to the pad, to the paint.
Friction.
When we are discussing the ability to polish paint we are discussing friction. Friction is what removes material and allows us to create a more level, more reflective surface. In this case friction will be determined by the pressure and velocity (distance over time) in which the pad is driven across the paint. The abrasives themselves (which are the final link between the machine's motor and the paint) do not care the direction they are being driven (whether rotational, straight line, orbital, or figure eight). We are not discussing the finish (evenness of the surface) they create, only the ability to remove material. Since pressure is a variable we cannot account for, we will focus on whether a DA polisher can move the abrasive with enough force to remove material (polish paint) with out rotating to answer the question: Does the pad have spin (rotate) in order to polish the paint when using a Dual-Action Random Orbital polisher.
A rotary polisher, because of its design and the way it drives the pad in a linear rotational manner, is very efficient at transferring the power of the motor to the paint surface. Like a drag slick that initially wrinkles on launch, a foam polishing pad on a rotary will absorb some of the initial acceleration of the pad. Once the pad is stretched to the max (under tension) and centrifugal force pulls the pad taut, much of the power is directly transferred.
A Random Orbital Dual-Action polisher, on the other hand is driving the pad in two different patterns simultaneously. The pad itself is subjected to a lot of flexing, and in turn, absorbs a lot of the orbital motion from reaching the paint. Like a bowl of Jello that jiggles on itself, the spongy nature of a foam pad can reduce the amount of energy transferred to the paint. Most DA polishers designed for automotive paint polishing have an orbital size of 5/16ths of an inch. If used with a tall, soft, large foam pad, as much as 80% of that movement can be absorbed inside the pad itself, and never reach the paint, where it is converted into useful paint polishing friction.
Friction as a form of pad speed.
Most DA polishers have a stroke or throw of 5/16ths of an inch. That means the diameter of each orbit is 5/16ths of an inch or 0.3125 of an inch. The total distance a point on the backing plate moves is 0.98125 of an inch for each orbit. Assuming that the pad transfers 100% of the movement of the backing plate to the paint, this means that each spot on the pad is moving nearly an inch per orbit. A random orbital DA polisher with a maximum speed of 6800 OPM (Orbits Per Minute) will drive every spot on the pad nearly 6,800 inches per minute with out the pad rotating one time. This is a speed of nearly 6.5 mph, constantly applied with pressure through out the entire surface of the pad. (As opposed to a rotating pad that will see significantly higher speeds on the outer edges but slow considerably as you approach the axis).
How much speed does rotation add? A DA polisher, when subjected to the down-pressure necessary to compress the pad (and ensure an efficient transfer of power through the foam) may rotate 1 time per second (this may be slightly faster than normal if you draw a line on the backing plate and watch). On a 5 inch pad with would add an additional 15.7 inches of distance per second or 942 inches per minute at the outer edge of the pad. This bumps our pad speed up to almost 7.3 mph, or slightly more than a 10% increase in polishing power, at the outer edge. When you consider that this advantage shrinks as we approach the center of the pad (2 inches from the axis we are only adding an additional 377 inches per minute) the net effect is small.
So does pad rotation offer a benefit?
Yes, pad rotation does offer some benefit in terms of typical DA polisher application. My rotating the pad you are creating a constantly changing (random) pattern on the paint that is exposing the paint to different and fresh abrasives. The random orbital action also dislodges the abrasives from the pad, where are they are free to rolls across the paint before reattaching in a new location/position. The increased speed of the pad rotation does offer some additional friction, usually no more than 10-20%. Additionally, some rotation will pull the pad tauter and make it firmer, which will allow more of the energy of the orbital movement to transfer to the paint.
The transfer of movement (energy) from the backing plate to the paint surface.
Foam polishing pads are similar to sponges in that they will absorb some of the orbital (not rotational, accept during acceleration) motion that is vital to a DA polisher correcting the paint. If you have polished with DA polish and remove the pad immediately after polishing you will notice that the backing plate interface is often warm or hot. This is a direct result of the flex (absorption of movement) of a foam pad. On a rotary polish the pad's surface (paint/paint interface) is often warmer do to the more efficient transfer of energy.
The taller (thicker) and larger (diameter) the pad, the more energy is absorbed through the greater surface area. This is one reason why smaller pads tend to work better with DA polishers. Smaller pads transfer more energy (by default) and place less drag on the pad, which allows for either more down-pressure to applied while maintaining pad speed or more more pad speed with similar pressure.
Most polishing foam pads have been adopted for use with a DA polisher. Recently advances in DA pad design have improved the ability of these machines to take full advantage of their potential. Lake Country's thin pads and Meguiar's DA Microfiber pads both feature a thin design that efficiently transfers the motion of the machine to the paint.
In conclusion.
With a larger pad, rotational speed is necessary to generate friction. As new designs of pad emerge that take advantage of the orbital motion, the rotation becomes less necessary as the bell curve for optimum performance shifts more to the orbital action. It is not necessary for a pad to rotate to generate the friction needed to remove paint defects or create a level surface, although it does offer a greater benefit with a larger, less efficient pad.
In practice.
The test section of this soft black hood was polished using a DA polisher. Steps where taken to correct the paint using little-to-no pad rotation. Step one was a 6.5 inch Lake Country Orange Pad with speed 5 and firm pressure. Step two was a 6.5 inch Lake Country Euro Green Pad with Blackfire SCR Finishing Polish and Speed 4.
Dual-Action Polishers are unique machines that rely on a multitude of simple physics in order to perform their job. Their job? In our world, DA (Dual-Action) polishers are used to polish paint. Polishing paint refers to the ability to remove material (in this case microscopic amounts of paint) in order to create a more level surface that reflects evenly. What gives a DA polisher its name is it's ability to move the pad in two different paths at the same time: In an eccentric or orbital pattern as well as a rotational pattern.
Random Orbital DA polishers only drive the orbital movement of the backing plate and pad. The rotation of the pad is a secondary movement, which is created by the inertia of the orbiting pad.
To understand the above concept imagine that you are holding a string straight above your head. Attached to the end of the string is a tennis ball. In order to swing the ball in a circle above your head you begin to spin your hand in tiny circles. Since you cannot dislocate your wrist and rotate it, you move your arm in an orbital motion. The inertia from your orbiting hand causes the ball to rotate above your head.
Another (more accurate) analogy is bicycle pedals. Bicycle pedals are attached to an arm that runs from center axis to the pedal. They orbital around the center axis because of the offset. If you jack a bicycle in the air by the frame (or lift up on the seat) so that the drive wheel is not touching and begin to 'pedal' the bike quickly with your hand you will notice that the pedal on the opposite side of the bike will begin to spin (in addition to orbiting around the axis).
The picture below illustrates the difference between an orbital movement and a rotational movement.
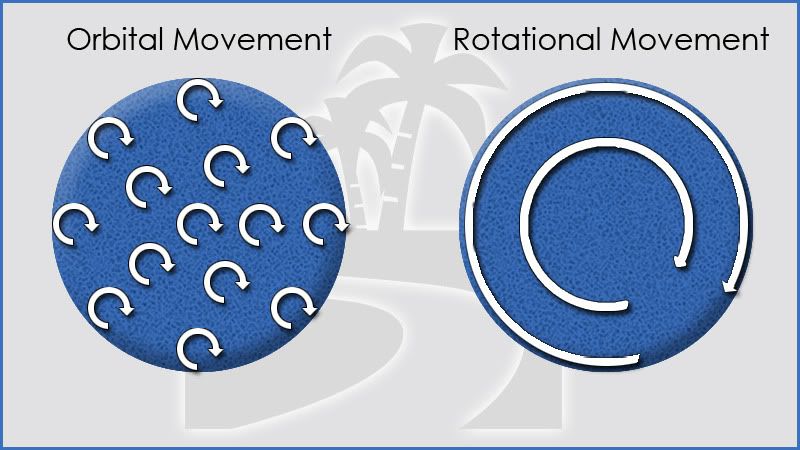
When we are polishing paint, in simple terms, we are trying to convert the the energy created by the motor of the machine into friction that removes paint. With a Dual-Action polish the energy is transferred to the drive arm (which orbits around the axis of the motor), through a bearing (which allows the pad to spin independently of the motor), to the backing plate, through the hook and loop, through the pad, and finally to the abrasives which are attached to the pad, to the paint.
Friction.
When we are discussing the ability to polish paint we are discussing friction. Friction is what removes material and allows us to create a more level, more reflective surface. In this case friction will be determined by the pressure and velocity (distance over time) in which the pad is driven across the paint. The abrasives themselves (which are the final link between the machine's motor and the paint) do not care the direction they are being driven (whether rotational, straight line, orbital, or figure eight). We are not discussing the finish (evenness of the surface) they create, only the ability to remove material. Since pressure is a variable we cannot account for, we will focus on whether a DA polisher can move the abrasive with enough force to remove material (polish paint) with out rotating to answer the question: Does the pad have spin (rotate) in order to polish the paint when using a Dual-Action Random Orbital polisher.
A rotary polisher, because of its design and the way it drives the pad in a linear rotational manner, is very efficient at transferring the power of the motor to the paint surface. Like a drag slick that initially wrinkles on launch, a foam polishing pad on a rotary will absorb some of the initial acceleration of the pad. Once the pad is stretched to the max (under tension) and centrifugal force pulls the pad taut, much of the power is directly transferred.
A Random Orbital Dual-Action polisher, on the other hand is driving the pad in two different patterns simultaneously. The pad itself is subjected to a lot of flexing, and in turn, absorbs a lot of the orbital motion from reaching the paint. Like a bowl of Jello that jiggles on itself, the spongy nature of a foam pad can reduce the amount of energy transferred to the paint. Most DA polishers designed for automotive paint polishing have an orbital size of 5/16ths of an inch. If used with a tall, soft, large foam pad, as much as 80% of that movement can be absorbed inside the pad itself, and never reach the paint, where it is converted into useful paint polishing friction.
Friction as a form of pad speed.
Most DA polishers have a stroke or throw of 5/16ths of an inch. That means the diameter of each orbit is 5/16ths of an inch or 0.3125 of an inch. The total distance a point on the backing plate moves is 0.98125 of an inch for each orbit. Assuming that the pad transfers 100% of the movement of the backing plate to the paint, this means that each spot on the pad is moving nearly an inch per orbit. A random orbital DA polisher with a maximum speed of 6800 OPM (Orbits Per Minute) will drive every spot on the pad nearly 6,800 inches per minute with out the pad rotating one time. This is a speed of nearly 6.5 mph, constantly applied with pressure through out the entire surface of the pad. (As opposed to a rotating pad that will see significantly higher speeds on the outer edges but slow considerably as you approach the axis).
How much speed does rotation add? A DA polisher, when subjected to the down-pressure necessary to compress the pad (and ensure an efficient transfer of power through the foam) may rotate 1 time per second (this may be slightly faster than normal if you draw a line on the backing plate and watch). On a 5 inch pad with would add an additional 15.7 inches of distance per second or 942 inches per minute at the outer edge of the pad. This bumps our pad speed up to almost 7.3 mph, or slightly more than a 10% increase in polishing power, at the outer edge. When you consider that this advantage shrinks as we approach the center of the pad (2 inches from the axis we are only adding an additional 377 inches per minute) the net effect is small.
So does pad rotation offer a benefit?
Yes, pad rotation does offer some benefit in terms of typical DA polisher application. My rotating the pad you are creating a constantly changing (random) pattern on the paint that is exposing the paint to different and fresh abrasives. The random orbital action also dislodges the abrasives from the pad, where are they are free to rolls across the paint before reattaching in a new location/position. The increased speed of the pad rotation does offer some additional friction, usually no more than 10-20%. Additionally, some rotation will pull the pad tauter and make it firmer, which will allow more of the energy of the orbital movement to transfer to the paint.
The transfer of movement (energy) from the backing plate to the paint surface.
Foam polishing pads are similar to sponges in that they will absorb some of the orbital (not rotational, accept during acceleration) motion that is vital to a DA polisher correcting the paint. If you have polished with DA polish and remove the pad immediately after polishing you will notice that the backing plate interface is often warm or hot. This is a direct result of the flex (absorption of movement) of a foam pad. On a rotary polish the pad's surface (paint/paint interface) is often warmer do to the more efficient transfer of energy.
The taller (thicker) and larger (diameter) the pad, the more energy is absorbed through the greater surface area. This is one reason why smaller pads tend to work better with DA polishers. Smaller pads transfer more energy (by default) and place less drag on the pad, which allows for either more down-pressure to applied while maintaining pad speed or more more pad speed with similar pressure.
Most polishing foam pads have been adopted for use with a DA polisher. Recently advances in DA pad design have improved the ability of these machines to take full advantage of their potential. Lake Country's thin pads and Meguiar's DA Microfiber pads both feature a thin design that efficiently transfers the motion of the machine to the paint.
In conclusion.
With a larger pad, rotational speed is necessary to generate friction. As new designs of pad emerge that take advantage of the orbital motion, the rotation becomes less necessary as the bell curve for optimum performance shifts more to the orbital action. It is not necessary for a pad to rotate to generate the friction needed to remove paint defects or create a level surface, although it does offer a greater benefit with a larger, less efficient pad.
In practice.
The test section of this soft black hood was polished using a DA polisher. Steps where taken to correct the paint using little-to-no pad rotation. Step one was a 6.5 inch Lake Country Orange Pad with speed 5 and firm pressure. Step two was a 6.5 inch Lake Country Euro Green Pad with Blackfire SCR Finishing Polish and Speed 4.
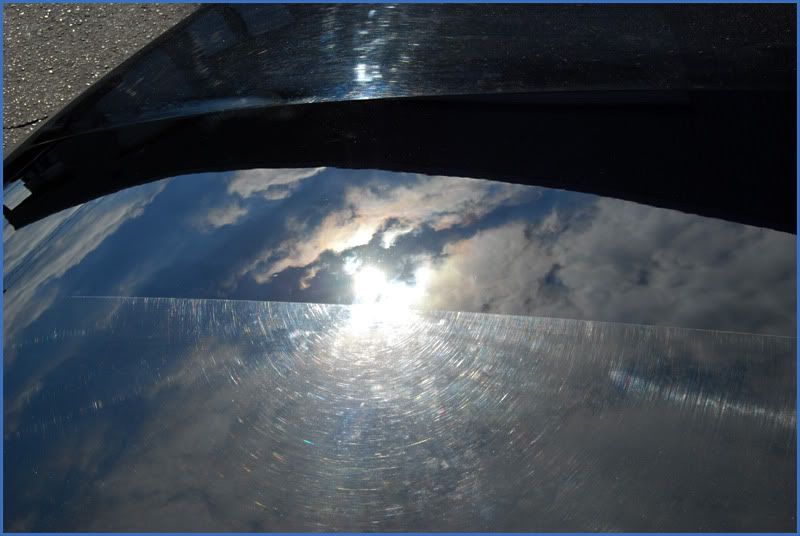
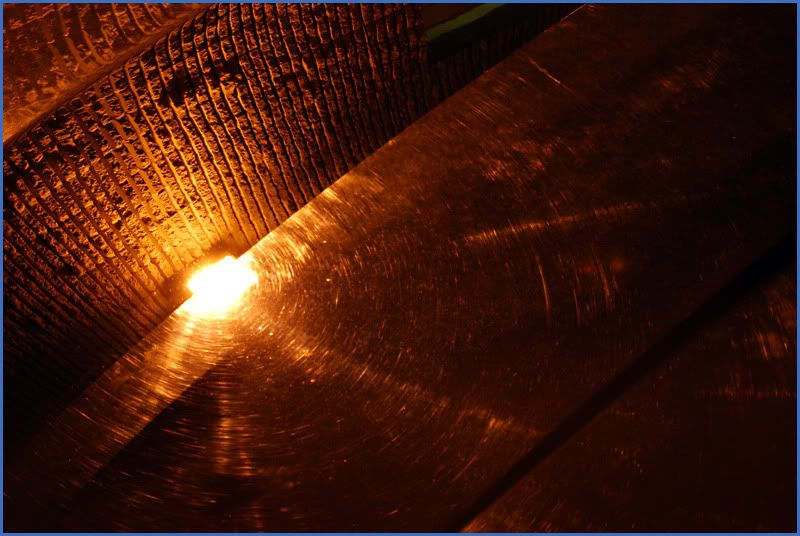