Todd@RUPES
Just a regular guy
Foam polishing pads have been around for almost 50 years, perhaps longer. The oldest types I have seen were made by Meguiar's, although I have spoke to several people who assure me they used off brand foam pads back in the late 1950's.
Today foam polishing pads are used for both machine and hand application of polishing compounds, waxes, glazes, and other surface treatment. Despite the overwhelming popularity of foam in the detailing industry it is often misunderstood. The purpose of this article is to clarify some rumors and share some of the information I have learned about foam (particularly as it relates to machine polishing) over my years in this industry.
The foam used on your polishing pad is measured in three main ways and has different classifications.
The first measurement is known as the PPI, or pores per inch. Foam is a highly textured network of foam membrane with large air gaps between the membranes (known as cells or pores). One simple measurement of the foam is too simply count (on average) how many pores there are per square inch.
The second measurement of foam is the measurement of the foam's firmness. This is measured using a standard measurement value called IFD (Indentation Force Deflection). An IFD number represents the pounds of force required to indent a particular size of the foam sample by a specified percentage of its
original thickness. Ultimately it is this measurement (or the one below) that most gauges the amount of cutting force the foam is going have.
The third measurement, which is similar in nature to the one above and the one most commonly used to measure polishing foams is known as CFD (Compression Force Deflection). CFD is the force in pounds required to compress an entire sample surface area to 50% sample height deflection. For both IFD and CFD measurements special test equipment is used.
PPI (Pores Per Inch)
PPI is a good way to catalog different foams that have similar performance. It is a relatively simple concept to grasp and is often quoted by the manufacturer. In general, although not always true, foams with a lower PPI are going be coarser and denser and provide more cut. Foams with a higher pore count are going to be softer, flex more, and provide less cut.
Measuring foams by quoting the PPI only tells a small fraction of the story. The pictures below represent two foams that each have 40 pores. Assuming that each picture is a zoomed to the point of a square inch, we could say that each foam has a PPI of 40.
The first foam...
The foam above has a pore count of 40 PPI. However it has small pores with a lot of membrane thickness between each pore. This will give the foam increased stiffness and increase the surface area that abrasives can attach too.
The second foam...
The above also has a pore count of 40 PPI. However it has larger pores with less membrane thickness between each pore. This will result (assuming the actual foam fiber is similar to the above example) in a foam that is softer and has less active surface area.
It is possible to have two foams, with similar formulas, with similiar PPI that produce radically different results. While PPI remains the most popular measurement to reference different foams by, it's usefulness is really limited in gauging the foam's performance.
IFD and CFD (Indentation Force Deflection and Compression Force Deflection)
PPI is a measurement of the foam's design, both the IFD and CFD are measurements of the foam's performance. PPI would be similar to the type of engine you are running: A turbo 4 cylinder or a large V8. IFD and CFD are a measurement of how that particular engine, in that particular car, performs . How fast does it get from 0-60, 1/4 mile, around a corner. Since the IFD and CFD measure the performance of the foam they give us a better understanding of how the foam will perform.
IFD (Indentation Force Deflection) is usually used to measure larger or softer foams, such as foams used in furniture or mattresses. Specially calibrated equipment is used to measure how much force is required to compress the foam different amounts, usually at 25% compression and 65% compression. This forums and accurate measurement of the foam since foam requires more force the more it is compressed. The IFD measures a specified area of the foam.
CFD (Compression Force Deflection) is used to measure small foams or very firm foams. It is a measurement of the force required to compress then entire piece of foam (instead of a smaller size of the foam like IFD). My measuring the amount of force required to compress the foam a very accurate measurement of the foams performance can be assessed.
Both the IFD and CFD measure the foam's firmness (willingness to compress) which has a dramatic effect on how much cut the foam will have when used to machine polish. Firm foam will create more friction on the paint's surface, and focus more friction on high spots, which creates more cut. But there is more to the foam's firmness that determines the how a foam will perform.
The intangibles:
As mentioned above, measuring the foam's firmness (in the case of polishing foams using the CFD measurement) is the most accurate measurement in gauging a foam's performance. There are other intangibles that effect how a foam will perform during machine polishing. These include how the foam caused the abrasives in the polish to interact with the paint, how well the foam cleans the paint of spend polish residue (squeegeeing effect of the membrane across the paint) and how many abrasives the foam can engage at one time. These intangibles are a result of many different areas of the foam's construction; below we will examine two different types of forum construction.
Closed Cell Construction vs. Open Cell Construction:
One of the biggest differences in foam types is the actual frame work surrounding each cell (pore). The pores are created when air bubbles form inside the foam as it is being cooked. The bubbles become closed pores (or closed cells). If the bubbles burst they become open cells.
A closed cell foam is much like a lot of tiny ping-pong balls joined together. A wall of membrane surrounds most of all of the surface of the cell. This is best illustrated in the picture of balls below.
An open celled foam is much more similar to a lattice network of netting. The cells are the pockets of air between the membranes and they twist and bend to create a frame. This is illustrated roughly in the photo of the finishing net below.
Closed cell foams tend to be slightly more aggressive (due to the increase in firmness or CFD) then open celled foams of a similar formula. Because each cell is closed air can not flow through the pad as readily, which keeps water based polishes from evaporating or drying out. The lack of air flow will cause the foam to hold more heat however. Polishing liquids will not wick (absorb) as quickly through the closed cells; more product is kept on the surface. Because there is less flex due to the increase in framework of a closed cell pad the more is more prone to tearing. This is particularly true of firmer foam formulas such as cutting pads. It also takes considerably longer for a closed cell pad to dry after being washed and they should not be used damp.
Open celled foams have the benefit of moving air through out the pad while polishing. This dissipates the heat created by the friction of machine polishing efficiently. The cell structure resembles lattice work or netting which gives an open celled foam more flex. The usual result is a less aggressive polishing action, particularly when used on a dual-action orbital polisher (due to the frequent twist, acceleration, and deceleration created by the movement of the machine).
Putting it all together:
Wall thickness, membrane structure, CFD, PPI, and cell structure are all important aspects when measuring and analyzing foam, but what is more important is how does the foam perform when you use it. This thread was intended to be informative and help explain how foam works as well as how it is measured. In the end though, after all the thought has gone into making the foam and the engineering and cutting of the foam is done by the manufacturer, what matters is what kind of results you achieve.
Thankfully the manufacturers use all if this information (and much more!) in creating polishing pads that continue to increase in performance (both cut and finishing ability) and make it easy for us to get great results.
Today foam polishing pads are used for both machine and hand application of polishing compounds, waxes, glazes, and other surface treatment. Despite the overwhelming popularity of foam in the detailing industry it is often misunderstood. The purpose of this article is to clarify some rumors and share some of the information I have learned about foam (particularly as it relates to machine polishing) over my years in this industry.
The foam used on your polishing pad is measured in three main ways and has different classifications.
The first measurement is known as the PPI, or pores per inch. Foam is a highly textured network of foam membrane with large air gaps between the membranes (known as cells or pores). One simple measurement of the foam is too simply count (on average) how many pores there are per square inch.
The second measurement of foam is the measurement of the foam's firmness. This is measured using a standard measurement value called IFD (Indentation Force Deflection). An IFD number represents the pounds of force required to indent a particular size of the foam sample by a specified percentage of its
original thickness. Ultimately it is this measurement (or the one below) that most gauges the amount of cutting force the foam is going have.
The third measurement, which is similar in nature to the one above and the one most commonly used to measure polishing foams is known as CFD (Compression Force Deflection). CFD is the force in pounds required to compress an entire sample surface area to 50% sample height deflection. For both IFD and CFD measurements special test equipment is used.
PPI (Pores Per Inch)
PPI is a good way to catalog different foams that have similar performance. It is a relatively simple concept to grasp and is often quoted by the manufacturer. In general, although not always true, foams with a lower PPI are going be coarser and denser and provide more cut. Foams with a higher pore count are going to be softer, flex more, and provide less cut.
Measuring foams by quoting the PPI only tells a small fraction of the story. The pictures below represent two foams that each have 40 pores. Assuming that each picture is a zoomed to the point of a square inch, we could say that each foam has a PPI of 40.
The first foam...
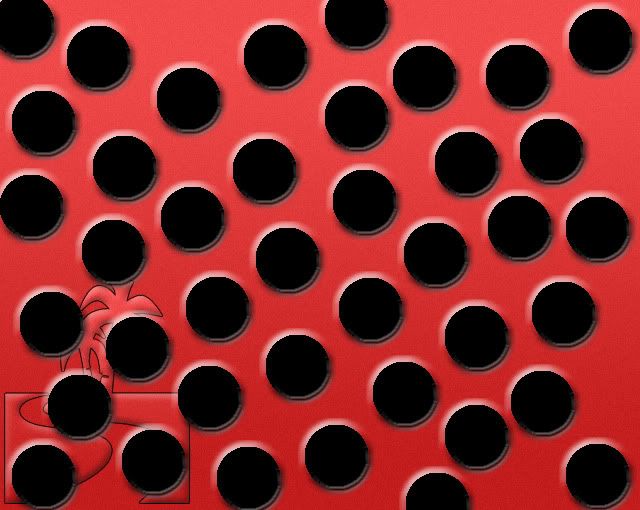
The foam above has a pore count of 40 PPI. However it has small pores with a lot of membrane thickness between each pore. This will give the foam increased stiffness and increase the surface area that abrasives can attach too.
The second foam...
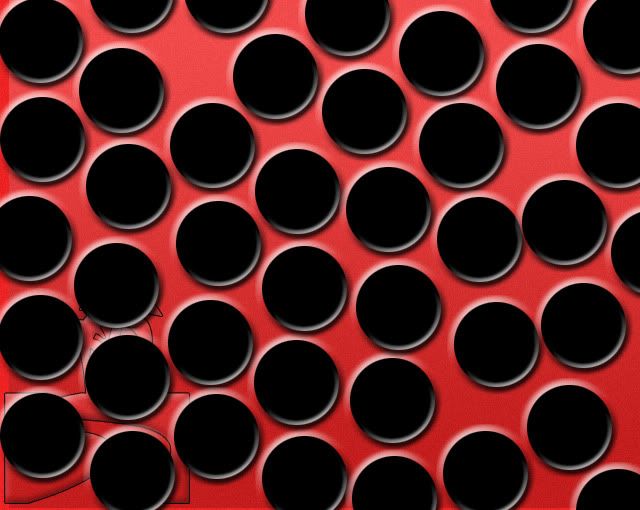
The above also has a pore count of 40 PPI. However it has larger pores with less membrane thickness between each pore. This will result (assuming the actual foam fiber is similar to the above example) in a foam that is softer and has less active surface area.
It is possible to have two foams, with similar formulas, with similiar PPI that produce radically different results. While PPI remains the most popular measurement to reference different foams by, it's usefulness is really limited in gauging the foam's performance.
IFD and CFD (Indentation Force Deflection and Compression Force Deflection)
PPI is a measurement of the foam's design, both the IFD and CFD are measurements of the foam's performance. PPI would be similar to the type of engine you are running: A turbo 4 cylinder or a large V8. IFD and CFD are a measurement of how that particular engine, in that particular car, performs . How fast does it get from 0-60, 1/4 mile, around a corner. Since the IFD and CFD measure the performance of the foam they give us a better understanding of how the foam will perform.
IFD (Indentation Force Deflection) is usually used to measure larger or softer foams, such as foams used in furniture or mattresses. Specially calibrated equipment is used to measure how much force is required to compress the foam different amounts, usually at 25% compression and 65% compression. This forums and accurate measurement of the foam since foam requires more force the more it is compressed. The IFD measures a specified area of the foam.
CFD (Compression Force Deflection) is used to measure small foams or very firm foams. It is a measurement of the force required to compress then entire piece of foam (instead of a smaller size of the foam like IFD). My measuring the amount of force required to compress the foam a very accurate measurement of the foams performance can be assessed.
Both the IFD and CFD measure the foam's firmness (willingness to compress) which has a dramatic effect on how much cut the foam will have when used to machine polish. Firm foam will create more friction on the paint's surface, and focus more friction on high spots, which creates more cut. But there is more to the foam's firmness that determines the how a foam will perform.
The intangibles:
As mentioned above, measuring the foam's firmness (in the case of polishing foams using the CFD measurement) is the most accurate measurement in gauging a foam's performance. There are other intangibles that effect how a foam will perform during machine polishing. These include how the foam caused the abrasives in the polish to interact with the paint, how well the foam cleans the paint of spend polish residue (squeegeeing effect of the membrane across the paint) and how many abrasives the foam can engage at one time. These intangibles are a result of many different areas of the foam's construction; below we will examine two different types of forum construction.
Closed Cell Construction vs. Open Cell Construction:
One of the biggest differences in foam types is the actual frame work surrounding each cell (pore). The pores are created when air bubbles form inside the foam as it is being cooked. The bubbles become closed pores (or closed cells). If the bubbles burst they become open cells.
A closed cell foam is much like a lot of tiny ping-pong balls joined together. A wall of membrane surrounds most of all of the surface of the cell. This is best illustrated in the picture of balls below.

An open celled foam is much more similar to a lattice network of netting. The cells are the pockets of air between the membranes and they twist and bend to create a frame. This is illustrated roughly in the photo of the finishing net below.

Closed cell foams tend to be slightly more aggressive (due to the increase in firmness or CFD) then open celled foams of a similar formula. Because each cell is closed air can not flow through the pad as readily, which keeps water based polishes from evaporating or drying out. The lack of air flow will cause the foam to hold more heat however. Polishing liquids will not wick (absorb) as quickly through the closed cells; more product is kept on the surface. Because there is less flex due to the increase in framework of a closed cell pad the more is more prone to tearing. This is particularly true of firmer foam formulas such as cutting pads. It also takes considerably longer for a closed cell pad to dry after being washed and they should not be used damp.
Open celled foams have the benefit of moving air through out the pad while polishing. This dissipates the heat created by the friction of machine polishing efficiently. The cell structure resembles lattice work or netting which gives an open celled foam more flex. The usual result is a less aggressive polishing action, particularly when used on a dual-action orbital polisher (due to the frequent twist, acceleration, and deceleration created by the movement of the machine).
Putting it all together:
Wall thickness, membrane structure, CFD, PPI, and cell structure are all important aspects when measuring and analyzing foam, but what is more important is how does the foam perform when you use it. This thread was intended to be informative and help explain how foam works as well as how it is measured. In the end though, after all the thought has gone into making the foam and the engineering and cutting of the foam is done by the manufacturer, what matters is what kind of results you achieve.
Thankfully the manufacturers use all if this information (and much more!) in creating polishing pads that continue to increase in performance (both cut and finishing ability) and make it easy for us to get great results.